The Enduring Gifts of Deming to the Purchasing Profession, Part 1
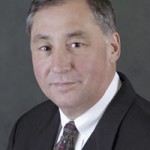
Robert Menard,
Certified Purchasing Professional,
Certified Professional Purchasing Consultant, Certified Green Purchasing Professional, Certified Professional Purchasing Manager
Editor’s note: This is Part One of a three part series on the powerful and pervasive influence of W. Edwards Deming on business in general and purchasing in particular. Click here for Part Two which explains the impact of the first 07 points on purchasing and click here for Part Three which explains the impact of the next 07 points on purchasing.
In business schools today, Supply Chain Management studies are growing in popularity, a curriculum that did not exist when I was in grad school. That is welcome progress. In my mentoring of grad students at University Texas at Dallas there is emphasis on current trends like Six Sigma, the ISO family of certifications, sustainability, and others.
Every quality program, whether Six Sigma, ISO, or other is an off shoot of the Total Quality Management (TQM) theory and practice developed by Dr. W. Edwards Deming. Deming has had as big an impact on global commerce as any other influential captain of industry in the 20th Century.
Deming’s iconic 14 Points of TQM were revolutionary when published in the 1940’s. Deming is considered by the Japanese to have had the greatest impact on business of any foreigner. Toyota was an early advocate of Deming’s work, a fact that no doubt contributed greatly to the subsequent rise and dominance of Toyota.
Although Deming died in his 90s two decades ago, his work lives on in the form of the Deming Institute and its “Deming System of Profound Knowledge”, a 503(c)(3) tax-exempt nonprofit organization. According to the Deming Institute, below the Deming Institute introduction (in italics) are his 14 Points of Total Quality Management.
“W. Edwards Deming offered 14 key principles for management to follow for significantly improving the effectiveness of a business or organization. Many of the principles are philosophical. Others are more programmatic. All are transformative in nature. The points were first presented in his book Out of the Crisis. Below is the condensation of the 14 Points for Management as they appeared in the book.”
We introduce them here and will comment on each in Part Two of this series.
1. Create constancy of purpose toward improvement of product and service, with the aim to become competitive and to stay in business, and to provide jobs.
2. Adopt the new philosophy. We are in a new economic age. Western management must awaken to the challenge, must learn their responsibilities, and take on leadership for change.
3. Cease dependence on inspection to achieve quality. Eliminate the need for inspection on a mass basis by building quality into the product in the first place.
4. End the practice of awarding business on the basis of price tag. Instead, minimize total cost. Move toward a single supplier for any one item, on a long-term relationship of loyalty and trust.
5. Improve constantly and forever the system of production and service, to improve quality and productivity, and thus constantly decrease costs.
6. Institute training on the job.
7. Institute leadership (see Point 12 and Ch. 8). The aim of supervision should be to help people and machines and gadgets to do a better job. Supervision of management is in need of overhaul, as well as supervision of production workers.
8. Drive out fear, so that everyone may work effectively for the company (see Ch. 3).
9. Break down barriers between departments. People in research, design, sales, and production must work as a team, to foresee problems of production and in use that may be encountered with the product or service.
10. Eliminate slogans, exhortations, and targets for the work force asking for zero defects and new levels of productivity. Such exhortations only create adversarial relationships, as the bulk of the causes of low quality and low productivity belong to the system and thus lie beyond the power of the work force.
•Eliminate work standards (quotas) on the factory floor. Substitute leadership.
•Eliminate management by objective. Eliminate management by numbers, numerical goals. Substitute leadership.
11. Remove barriers that rob the hourly worker of his right to pride of workmanship. The responsibility of supervisors must be changed from sheer numbers to quality.
12. Remove barriers that rob people in management and in engineering of their right to pride of workmanship. This means, inter alia, abolishment of the annual or merit rating and of management by objective (see Ch. 3).
13. Institute a vigorous program of education and self-improvement.
14. Put everybody in the company to work to accomplish the transformation. The transformation is everybody’s job.