Supplier Plant Visit at the World’s Largest Volvo Truck Manufacturing Facility, Part 3
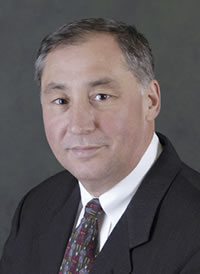
Robert Menard,
Certified Purchasing Professional,
Certified Professional Purchasing Consultant, Certified Green Purchasing Professional, Certified Professional Purchasing Manager
Editor’s note: This is the third part of a three part story about my visit to the Volvo plant in Virginia. Click here for Part 1 and here for Part 2 .
Energy Efficiency
Volvo Truck’s goal at the NRV plant is to reduce energy consumption. Substantial efforts have been made in retrofitting the nearly four decade’s old plant to save energy. Insulated sky lights are everywhere. Not only do they save large amounts of energy using natural light but the daylight has a positive, upbeat, and motivating impact on employees. No one is trapped inside a behemoth plant for a third of the day without the stimulation of sunlight.
Another practical and effective energy savings investment is the use of infra-red heat at loading doors. Many plants with hundreds of doors for at receiving and loading docks still deploy forced heated or cooled air heated in a losing battle to combat Mother Nature’s overwhelming superiority. The dock seals were in such good shape that I could not see daylight sneaking in so very little conditioned air escapes.
In typical infra-red systems, natural gas is ignited along the length of 3 to 4 inch diameter tubes. The heat energy radiates in all directions but shiny steel lenses in semi-circular (sometimes parabolic) shape collect all the energy headed elsewhere and reflect it down toward the floor. Ideally, the “infra-red czne” heats the floor space most occupied by workers.
Infra-red technology is so effective because it heats the mass, such as boxes of product, concrete floors, machinery, equipment, and people, not the air. I have seen infra-red applications in much more severe climates such as a distribution center in Ontario. I visited one in the 1980s to decide about using this new technology for a client. The dock workers were in shirts, not jackets, on a day where the outside temperature was about – 20C, or about 0F. The next morning, the workers were grousing that the place was cold because the overnight shift had loaded out about 40 trailers and much of the stored heat went out the loading dock door in boxes of product. The concrete slab was warm but the difference on the skin was palpable.
More Best Practices
The value of ergonomics is embraced by everyone at NRV. Environmental Health & Safety is a gold mine for business, labor, and government. Workers who suffer fewer and less serious injuries and illnesses are happier and more motivated. They also increase productivity so ergonomics is an all-around winner. Chairs and work station furniture are designed around the task. Robots handle many of the repetitive motion tasks that would otherwise pose risks to workers.
Just-in-Time (JIT) techniques are everywhere at NRV. The ASRS is one example but that is largely hidden from view. The tire mounting and assembly is far more dramatic. Forklifts unload many trailers full of tires from various manufacturers (sometimes specified by customers) and deliver them in a matter of minutes to nearby mounting and inflation stations. The tires are then picked up by a robot that slips them onto axle assemblies where they are secured. The entire axle/wheel sub unit is then installed upon a chassis frame which is upside down on a moving platform in order to ease labor and ergonomic burdens. Finally, the assembled chassis unit is flipped around so the ever growing truck can roll along until the minutes old truck is fueled and driven off the production line.
Summary
It is the assimilation of the technological and of the creative energies, directed by smart dedicated people under visionary leadership that distinguishes the NRV plant. It is a company’s leadership that picks the management which executes the strategy that brings success.
The deployment of best practices like kanbans and kaizen, developed in Japan under the tutelage of Dr. W. Edwards Deming after WW II and popularized by Toyota are foundational principles. Building upon Deming’s 14 points of Total Quality Management, the NRV plant has mastered lean manufacturing techniques.
None of this would be possible without the active and engaged input of employees of all stripes. Bravo NRV!
But the labor management partnership at NRV has not always been this strong as we shall see soon.