New Technologies for (Portland) Cement
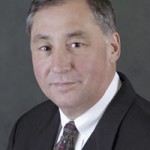
Robert Menard
Certified Purchasing Professional,
Certified Professional Purchasing Consultant, Certified Green Purchasing Professional, Certified Professional Purchasing Manager
In the late 1990s and early 2000s, I was fortunate to serve the Portland Cement Association by writing and delivering several multiple day seminars. Having an undergraduate degree in Civil Engineering and experience in the construction industry, as well as extensive practice in supply chain management, serving the PCA was a comfortable experience for both parties. I had the good fortune to meet many cement company executives that resulted in service to many cement and concrete companies.
Having enjoyed the learning experience of multiple visits to cement plants, distribution facilities, and logistics methods, I became thoroughly schooled in the chemical and physical processes need to transform raw limestone from the quarry to finished cement in the silos. As a Certified Green Purchasing Professional, I remain very cognizant of the scream from so-called “environmentalists” that each ton of cement releases one ton of CO2 into the atmosphere. Therefore, my sensitivity to new technologies in cement production always grabs my attention.
Of late, interest in carbon sequestration , particularly as it affects cement has risen in publicity. For the sake of focus, we will not delve into the arguments of whether CO2, necessary for life, is a pollutant or whether it contributes to global warming. Neither of these arguments is resolvable. Nor shall we drill too far down on the chemical processes involved in carbon sequestration. Those with interest can research it independently.
Another technology was highlighted in a November edition of ENR “Materials” story. It starts by downplaying the use of sequestration and fly ash then introduces Solidia Technologies a NJ based private company specializing in “green” concrete. Solidia is partnering with France based Lafarge the world’s largest cement producer to bring CO2 cured cement to commercial scale.
The processes involved CO2 cured cement in differ significantly from traditional Portland cement production. In terms of energy, the kilns need only to be fired to 1,200C, 20% less than Portland cement kilns. The Solidia process uses CO2 as a catalyst to produce calcium carbonate. Solidia claims that its carbonization product is far more stable than the calcium hydration process of Portland cement.
Other significant differences
There are some great differences in composition. Portland cement is composed of 80% limestone and 20% shale, along with traces of bauxite, gypsum, iron, and other minerals. Solidia cement contains equal proportions of 50% limestone and shale. The story is silent on other trace minerals. Solidia claims that their CO2 emissions are less than 550kg per ton of cement versus the 800kg for Portland cement. Although the brief story does not elaborate, presumably the 31% reduction in greenhouse gas emissions is attributable to both the reduced limestone content and lower kiln temperatures. All this is good so far but isn’t there always a “but”?
But what are the downsides
For starters, nowhere on the web is any reference to the price per ton. It is safe to assume that the price is higher, perhaps much higher, per ton than Portland cement.
A larger issue though is the Solidia cement’s pH value. The pH of about 12 for most Portland cements makes it a very base or alkaline material. Although the ENR piece did not reveal the pH of Solidia cement, Solidia admits that its cement has a lower pH than traditional Portland, which contributes to the early oxidation of rebar the reinforcing steel used in reinforced concrete, by far the most widely used form of concrete.
Steel is used in concrete because concrete is about ten times stronger in compressive strength than in tensile strength so steel carries the tensile stresses.
A Solidia spokesperson, Dr. Richard Riman, distinguished professor of Rutger’s University’s dept. of Material Science and Engineering, and also a co-founder and chief scientist at Solidia calls the lower pH an “Achilles heel.” Riman further added that “We’re not going to be telling people to put rebar in this material until we have a solution that we know works. Plenty of products do not require rebar and we’re going there first.” Solidia has agreements with the Cooperative Research and Development Agreement (CRADA) with the U.S. Dept. of Transportation and the Federal Highway Administration to test non-reinforced structures such as curbs and barriers. If these tests prove out, perhaps other markets such as agricultural, dams, landfills will become viable. Although the ENR story was silent on other reinforcing material such as glass fibers, maybe this is already under consideration.
Will Solidia cement succeed?
“Quien sabe”, as we used to say in Latin class. Every innovation is not recognized as a historic watershed until it succeeds. Then, a long line forms of fathers claiming credit for the innovation. Within a short time lapse thereafter, the innovation slips into the world of common achievement.
Does Solidia cement have promise? Yes. Its success needs more time and experimentation. A little information on its price and costs benefits would not hurt either.