Purchasing Managers with Warehousing Responsibility
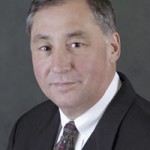
Robert Menard
Certified Purchasing Professional,
Certified Professional Purchasing Consultant, Certified Green Purchasing Professional, Certified Professional Purchasing Manager
Many of us in purchasing, particularly those in smaller companies, often have responsibility for warehouse operations. In that we in the purchasing world tend to have little training, we are often thrust into the warehouse with zero knowledge of how to manage this important responsibility.
Let me cite the case of a good client. It had two warehouses, referred to as “the larger and the smaller”. My client representative, the new Purchasing Manager, also had warehouse and inventory responsibility so we devoted ample time to unraveling the mess. He did not know why they had two warehouses. Both were disorganized, messy, and unsecured. Expensive portable (easily stolen) assets were strewn amongst copy paper, toilet paper, bottled water, and trash. Nothing was labeled by name and no bar codes existed. Many items were apparently dumped on the floor. Upon closer examination, much of the stock in this “Tomb of the Unknowns” was unusable, obsolete, or unidentifiable by current employees. Shelving was poorly organized. Worse yet, although the walk doors were controlled by key pad access, the overhead doors beside them were unlocked and easily opened.
Some parts were apparently bought and either not needed or not used. One carton bore a shipping date of nine months earlier and was shipped via 1 (next) day delivery. The box had never been opened.
Much smaller equipment was stored or perhaps abandoned outside a shop door. The shop manager identified them as junk that is scavenged for parts. These small assets ($1,000 or less) are generally not worth repairing as replacement is usually cheaper.
Larger walk behind and other machinery ($15,000 to $20,000) was slated for repair as time allowed and rotated in as time and personnel permit. However, the lack of identification, prioritization, and general informality portrays a system with little to no control.
No tags to identify specific problems needing attention were in evidence. Since there are so many units, an obvious question is “Who knows what needs to be done?”
Recommendations
- An ambitious campaign involving separate but related elements of management, inventory, security, technology, purchasing, accounting, and business controls must be implemented. Barcoding, appropriate software, upgraded technology, etc, are co-requisites. All stored assets must be labeled, tagged, and purged periodically.
- Without Item Numbers, there is no way to track how much money is being spent on individual units. It is possible that some units are repaired at costs in excess of replacement.
- Consolidate warehousing operations in the larger warehouse. Doing so would open up the space in the smaller warehouse to other purposes.
- Appoint a new receiver who should be located within the warehouse. Provide a modular office with climate control. These are routinely fitted with heavy weight bearing roofs for mezzanine storage.
- Store high value assets in a secured area as well as lower value items that would be subject to pilferage otherwise.
- All the tools of technology must be available. Some training may be required. Some of the main features of the new inventory system are:
- All incoming deliveries should be bar coded and bear PO Number and Part (Item) Number
- When swept by the reader wand, it should automatically be uploaded into inventory, the PO closed and payment scheduled
- Upon receipt of major purchases for jobs, received deliveries should be automatically credited to inventory and then debited to the job cost when it its barcode is swiped as it leaves the warehouse for delivery to the job.
7. An elevated loading dock may become necessary as suppliers change their delivery habits due to new negotiated agreements. Some delivery vehicles may not have lift gates and some may require (certainly, a 45 foot trailer forklift availability to unload. Hoisting equipment is needed in the warehouse in any event so this should not be a problem.
8. Some of existing shelving and racks are adequate for the moment but as material is increasingly relocated to the warehouse, new racks and shelving may be needed. To maximize the storage, this will mean that some material is stored out of visual and hand-accessible range.
9. A long established Warehouse Management System technique is to deploy a Radio Frequency Identification (RFID), sometimes called “proximity” system. A barcode request is input into the system and the retrieval vehicle (high-bay lift) is guided to the location. In large systems, the vehicle is guided automatically, but in small systems, an audible signal grows in intensity as the operator reaches the desired bin/pallet location is neared. Apropos, larger pallet size racks and shelving may be needed for pallet deliveries.
10. Essential elements of this system are orderliness, labels & signage, barcodes, and software. Also, parts storage bins should arrayed in an organized fashion on shelves. Each should bear the name and Item Number, manufacturer, and sometimes project number, either a jobsite or capital expenditure project. In many cases, voice recognition software allows items to be accessed using verbal commands.
Click here for a companion post, Purchasing Managers with Inventory Responsibility.